Get ready, we're about to dive deep into working with stainless steel for welding, fabrication, cutting, grinding, buffing & polishing, and everything in between.
This post starts off with a lot of information about what stainless steel is, how it's "stainless" and the different types of stainless steel. If you're in a rush and just want to get to the process you need, feel free to click one of these links to jump to that section of the page.
Skip Ahead:
- About Stainless Steel
- Welding Stainless Steel
- Abrasives to Enhance Stainless Steel Welding & Fabrication
- Finishing Stainless Steel
- Stainless Steel Do's and Don'ts
- Proper Abrasives Selection
About Stainless Steel
Why and where should you use stainless steel?
Stainless steel is used for its outstanding corrosion resistance in even very corrosive environments such as saltwater and acids. Stainless steel fabrication projects such as outdoor furniture, boat hardware, autobody parts, knives, and architectural railings will not corrode. Stainless steel is great for food preparation surfaces and utensils in your kitchen, restaurant, or food processing plant.
Unlike coated steel or aluminum, your fabrications made of stainless steel will be maintenance-free because:
- Stainless steels have superior corrosion protection and require no coatings
- Stainless steel’s corrosion protection is more than skin deep. If a stainless steel surface is scratched or eroded, the corrosion protection will self-repair or regenerate. If you scrape or wear the paint off a coated steel fabrication, then the steel will likely rust if there is moisture present.
Stainless steel has definite advantages over steel and aluminum. You will pay twice as much for stainless steel alloys compared to carbon steel, so you don’t want to use stainless everywhere. Also, stainless steel fabrication costs can be higher than steel and aluminum.
If your fabrication project is going to be sitting in a dry, indoor location, then you may not need stainless steel. A layer of paint or an epoxy coating on a steel workbench or indoor furniture will protect against corrosion. If you are making a tool or gage for your shop, then you can employ a film of oil or grease for protection. Steel with a zinc undercoating (galvanization) and protective top coating will prevent corrosion on outdoor projects, but not after the coating chips, delaminates, or is worn off the surface.
The aesthetics or beauty of stainless steel is another reason to use the metal in your fabrication projects. With the proper selection of abrasives, a wide variety of exquisite finishes can be generated on stainless steel.
What makes stainless steel “stainless”?
To understand what makes stainless steel “stainless”, you need to know a little bit about the composition of stainless steel.
The chromium ingredient in stainless steel is what makes stainless steel “stainless”. The chromium reacts with oxygen in the air to form a transparent “passive” layer of chromium oxide on the surface of stainless steel. Nickel additions to stainless steel also improve corrosion resistance. Steel needs at least 10.5% chromium to develop a passive oxide film and become stainless. Most stainless steel alloys have more than 12% chromium to maintain passivity and corrosion resistance after welding, casting, and other thermal processing.
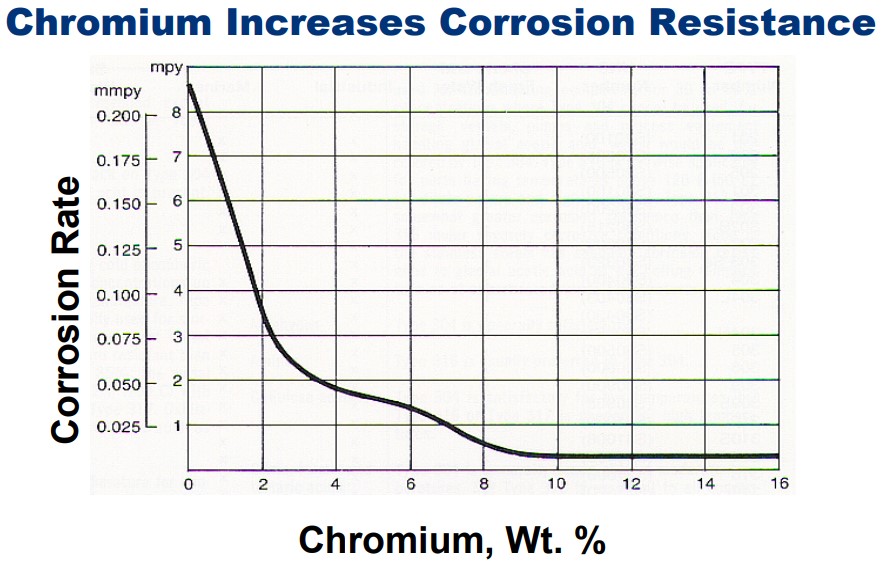
The chromium oxide layer is “tight” or non-porous and strongly bonded to the surface.
The passive layer forms a barrier isolating the metal from the environment and preventing further corrosion. The passive chromium oxide film on stainless steel is atomically thin - 0.0000001 inches (2.5 nanometers) thick.
When stainless steel is cut or ground, the passive film reforms instantly, which is why the corrosion resistance of stainless steel is self-repairing. Rust layers are oxide layers also. Most rust layers are soft and porous, so moisture and oxygen can pass through to continue to oxidize carbon steel.
The chromium oxide layer can be disrupted or contaminated during fabrication steps such as welding and grinding. Gentle abrasive finishing and passivation can re-passivate the metal. There are also chemical pickles and electrochemical methods to passivate stainless steel.
If your stainless steel parts are used in anaerobic conditions or liquids devoid of oxygen, then the passive film cannot reform and corrosion can accelerate. A coating or paint on stainless steel can block oxygen from getting to the surface for passive film renewal. NEVER PAINT STAINLESS STEEL.
The assembly process can also deteriorate the corrosion resistance of stainless steel. If your stainless steel parts are bolted together, then the areas under the nuts, washers, and bolt heads can be more susceptible to corrosion if oxygen cannot reach these surfaces to maintain passivity. Welding can also deteriorate the corrosion resistance of stainless steel by depleting or tying up the protective chromium.
A typical stainless grade like 304 is not much harder or stronger than carbon steel, so why is stainless steel more difficult to fabricate, grind, and finish?
While the additions of chromium and nickel improve corrosion resistance. These additions and the stainless steel’s nature can cause several fabrication difficulties such as:
- Stainless steel is trickier to weld requiring argon or inert gas to protect the reactive chromium and nickel.
- Stainless steel is more difficult to cut, machine, and grind than carbon steel because:
- Chromium is a reactive metal, so stainless steel tends to bind or stick to the edges of cutting tools or abrasive grain edges.
- Chromium oxide is slightly harder than aluminum oxide, which many abrasives are made of.
- Stainless steel has high ductility, so long chips are formed during cutting. Higher grindability and machinability alloys have chips that break into small pieces and can clear the cutting or grinding zone.
- Stainless steel has a “high strain hardening coefficient” or can be cold worked to high strengths, which means the metal gets harder when deformed or sheared during cutting or grinding.
- The extensive alloying reduces thermal conductivity, so heat cannot be dissipated through the metal during cutting and grinding.
- The chromium and nickel additions improve high-temperature strength, so the hotter stainless steel chips still require greater forces to cut or shear. The greater cutting forces further increase the heat at the cutting or grinding zone.
What types of stainless steel are there?
As with carbon and alloy steels, there are many different AISI grades of stainless steel.
Stainless steels can be grouped into five major families:
- Austenitic Grades – 304 or 316 stainless steel
- Ferritic Grades – 430 stainless steel
- Martensitic Grades – 410 or 440 stainless steel
- Precipitation Hardening Grades
- Duplex Grades
Austenitic Stainless Steels (304, 316)
Austenitic stainless steel has an austenitic metallurgical or crystal structure. The most widely used and available stainless steel grade, 304, has about 18% chromium and 8% nickel. 304 is also commonly known as “18-8”. Austenitic stainless steels have superior corrosion resistance, excellent weldability, and unusually good formability. They have only fair machinability and grindability.
While austenitic stainless steels are considered unhardenable grades, austenitic stainless steel can be cold worked or work hardened to ¼ hard, ½ hard, and full hard conditions. Cold working is when the metal is squeezed between two rolls in the cold rolling mill without preheating the metal. Cold forming or hammering stainless at room temperature with strain harden stainless as well.
Ferritic Stainless Steels (430, 409)
Ferritic stainless steel derives its name from its ferritic metallurgical structure, which results from the lack of any nickel. Ferritic grades are not hardenable. 430 is the most common ferritic stainless grade. Like austenitic stainless steels, ferritic stainless steels are highly formable but more difficult to grind. Welding ferritic stainless steel does not have easy at the austenitic alloys. 430 is easier to machine, blank, or shear than 304. Ferritic stainless steels are magnetic.
Martensitic Grade Stainless Steels (410, 440)
Martensitic stainless steels have higher carbon and lower nickel. They can be hardened by conventional quenching and tempering like tool steels or higher carbon alloy steels. 410 can be machined as well as hot or cold formed, but the high carbon 440 grades can only be hot formed. Machining and cold forming are not viable options for 440 grades. Martensitic stainless steels are easier to grind compared to austenitic and ferritic grades. Like the ferritics, martensitic alloys are not welded as easily as austenitic grades. Martensitic stainless steels are magnetic.
Precipitation Hardening
Precipitation Hardening can be softened in a solution heat treatment, formed and machined, and then age hardened to extremely high strengths. They are used to make landing gear components for aircraft and other highly stressed components.
Duplex Stainless Steels
Duplex stainless steels contain both ferrite and austenite. They are the newest stainless steel class. Certain grades in the duplex group have the highest corrosion resistance of any stainless steel. They can even exceed the excellent corrosion resistance of austenitic stainless steels. They are used in offshore oil, chemical plants, sour gas wells, and other demanding applications.
What stainless steel grades should I fabricate with?
304 Grade Austenitic Stainless Steel -
Austenitic 304 stainless steel is the most widely used grade of stainless steel. 304 is considered the general-purpose stainless grade.
304 stainless steel has excellent corrosion resistance, fantastic formability, and good weldability. 304 stainless steel is the alloy to select for most fabrication projects where the end-use is a wet or damp environment such as outdoors, near swimming pools, or in bathrooms or kitchens.
304 stainless steel is readily available. In fact, if you stop in a local metal service center or distributor and ask for stainless steel, 304 stainless is probably what you will get.
In short, if you want to bend, form, and fabricate outdoor architectural elements (ornaments, trim, gates, railings, handles), plumbing fittings, and bathroom/kitchen projects (tables, sinks, shelves, racks), then 304 is the best choice.
316 Grade Austenitic Stainless Steel -
316 is more passive or noble than 304 due to higher nickel levels and molybdenum additions. 316 stainless steel provides a step up in corrosion resistance, especially in salt water or chloride environments. 316 stainless steel is sometimes called marine-grade stainless steel. If you are fabricating a fishing pole holder, a custom extension table for a Magma grill, a mount for a GPS or sonar fish finder, or a fold-up table, then 316 stainless would be a better choice than 304. You will pay at least a 20 to 30% premium for 316 stainless steel. Austenitic stainless steels are non-magnetic.
If parts of your project are going to be welded together, then you want to use 304L and 316L grade stainless steel alloys that have lower carbon content, which prevents “sensitization” during welding. Sensitization is the depletion of the protective chromium through the formation of chromium carbides at the grain boundaries, which can result in intergranular corrosion.
If you are fabricating parts for a higher temperature application such as a barbeque grill or shop furnace, stainless steel will perform better than alloy or carbon steel. Austenitic grades 309 (23% chromium and 14% nickel) and 310 (25% chromium and 20% nickel) are designed to maintain strength and resist forming oxide scales at high temperatures. At red hot temperatures, even 304 stainless steel will do much better than carbon steel.
Martensitic Stainless Steels (410, 420, 440C) -
If you want to make a corrosion-resistant knife, blade, or tool with high hardness, then a hardenable martensitic 410, 420, or 440 grade stainless steel would work. 410 stainless steel can be formed to a degree, but martensitic parts are typically made using machining or grinding – especially the high carbon and high chromium 440 grades. If you are making a part out of martensitic steel, you should:
- Initially form, cut, or machine to create the rough shape using the martensitic steels in the annealed condition.
- Quench and temper to harden the martensitic stainless steel.
- Use abrasive grinding to generate the final shape.
- Finally, smooth and polishing with finer grit abrasives to generate the surface finish.
Ferritic stainless steels (430 and 409)
This grade of steel is commonly used to form automotive muffler and exhaust systems. They do have the corrosion resistance of austenitic stainless steel, but they are lower in cost. They are soft and easily formed, but more difficult to weld than austenitic stainless steel. They have good corrosion resistance in outdoor applications, but they do have high strength. Ferritic stainless steels like 430 and 409 are used to fabricate sinks, kitchen appliances, lower grade cutlery, stairs, mufflers, heaters, gutters, roofing panels, moldings, countertops, and ornamental work. If you want an alloy that is corrosion resistant and magnetic, then 430 ferritic might be suitable.
Automotive OEMs and industrial manufacturers use ferritic grades because they can save money. For most shop, or DIY projects, we would recommend using austenitic stainless steels on most of your projects.
If your design is a hit and you end up making hundreds or thousands of the same stainless parts, then investigate switching to ferritic grades like 430 or 409 to save money.
Stainless Steel Forming
Are stainless steels as formable and weldable as carbon steel?
Most stainless steels are very formable in the annealed or soft condition. Annealed or unhardened austenitic (304, 316), ferritic (430, 409), and 410 grade martensitic stainless steels can be cold formed with ease.
While 304 stainless can be easily formed in the annealed or soft condition, you will run into limitations in bending and forming a fully hard 304 stainless steel without cracking. You can purchase 304 stainless steel in annealed, ¼ hard, ½ hard, and full hard conditions. Full hard 304 stainless will have about twice the strength as annealed 304, but with much lower ductility, which will limit forming.
Annealed 304 sheets can be formed with a bend radius a small as half the metal’s thickness. You cannot cold form a full hard 304 sheet with a small bend radius without cracking the material. On a full hard 304 sheet, the minimum bend radius is three times the sheet thickness.
If you are going to deeply form your parts and weld, then you might as well use annealed 304 stainless. The heat from welding will anneal and soften the stainless steel outside the weld zone.
Welding Stainless Steel
Once your stainless parts are formed, they can be welded almost as easily as carbon steel. An inert gas or gas mixture is required if you are going to MIG or TIG weld. Argon-carbon dioxide gas mixture protects the chromium and nickel in the weld pool from oxidizing. Stainless is also welded using flux-cored wire and fluxed coated stick welding, but MIG and TIG will typically provide better results.
Bands of discoloration or “heat tint” can form outside the weld zone in the parent metal. Heat tint discoloration can appear as a rainbow of colors varying from yellow to blue. The discoloration is just a thicker layer of chromium oxide. Unfortunately, the formation of this thicker heat tint oxide depletes the protective chromium levels below the heat tint, which can result in rust. The heat tint oxides and some of the stainless steel below the heat tint must be removed to keep the metal “stainless.”
Similarly, the backside or root of the weld zone can discolor or “sugar”. “Sugaring” is a heavy oxide scale caused by oxidation in the weld zone. Sugaring has the appearance of wrinkled or shriveled black sugar. The backside of the parts can also heat tint – especially in weld joints with multiple passes. Back purging gases, fluxes, and a backing plate or ring can be used to prevent sugaring and heat tint.
We mentioned before that lower carbon versions of 304 and 316 alloy, 304L and 316L should be used in welded fabrications to prevent sensitization. Welding wires made with extra chromium (308 and 309) are also recommended to prevent chromium depletion. Sensitization and chromium carbide precipitation can also occur when welding stainless steel to carbon or alloy steel and ferritic or martensitic stainless steel. These higher carbon metals will cause depletion of chromium making the joint susceptible to corrosion.
Joining stainless and carbon steel is a bad idea even in a bolted joint because the metals have different electrochemical potential, which will cause accelerated corrosion of the lower potential carbon steel.
How do abrasives enhance stainless steel welding and fabrication?
Abrasives can be used to enhance several steps in the welding and fabrication process:
- Cutting stainless steel
- Deburring cut edges
- Preparing stainless steel surfaces for welding
- Removing heat tint and sugaring
- Cleaning and blending stainless steel welds
- Polishing to a brushed or satin finish
- Buffing to a polished or mirror finish
How to Cut Stainless Steel
Stainless steel sheet and plate can be cut into intricate 2D patterns using plasma cutters. Plasma cutters can be affordable, but you will have to send your parts out if want to use waterjet cutting or laser cutting.
If you are just cutting stainless steel into simple shapes from stock like sheet, plate, tube, or, bar, then you have several options:
- Tin snips or hand shears can be used to cut thinner stainless steel sheet.
- Power nibblers and power shear tools can cut slightly thicker stainless steel sheet.
- Metal shear presses can quickly shear off a large sheet or make a long straight cut across a thicker stainless steel sheet or plate. A shear capable of cutting ¼ inch carbon steel sheet will only be able to cut 3/16 inch thick stainless steel sheet. A large tonnage press can shear 1-inch thick stainless steel.
- Toothed saw blades mounted on band saws, reciprocating saws, or circular saws can cut bar, rod, tube, plate, and sheet.
- Abrasive cutting wheels mounted in chop saws, circular saws, and angle grinders are useful in cutting cut bar, rod, tube, and narrow plate.
If toothed saws are used to cut stainless steel, then they should be carbide-tipped saw blades (tungsten carbide teeth). Bi-metal high-speed steel-carbon steel blades may cut stainless steel, but they will not have the life and the straight cutting of carbide-tipped blades. While carbon steel can be cut with a saw blade speed of 270 feet/minute, 304 stainless steel should be cut at a slow speed of 115 feet/minute.
Holes are drilled or cut using drill bits or hole saws mounted in drill presses or power hand drills. Holes saws work well on sheet metal and thinner stainless plate. Drill bits are a better choice for thicker stock.
Ideally, cutting lubricant or coolants should be used when toothed saw cutting or drilling stainless steel. They will reduce friction and help cool the parts minimize discoloration.
While you can use a toothed carbide blade to cut stainless steel, an abrasive cutoff wheel will cut stainless faster. With thinner stainless sheet, tin snips or carbide-tipped saws are fine. When cutting thicker stainless steel bar, rod, angle iron, and other structural shapes, a cutoff wheel in a chop saw is the way to go. Apply steady, moderate pressure when cutting stainless steel with an abrasive wheel.
If you are using a cutoff wheel in an angle grinder, then be careful not to twist or bend the blade while cutting. Cutoff and grinding wheel can be broken. Thinner cutting wheel blades tend to cut cooler with minimum kerf.
Deburring Stainless Steel
Shearing, saw cutting, and abrasive cutoff wheels typically leave a sharp burr on the cut stainless steel edge. Drilled or saw cut holes also tend to have burrs. The sharp burrs can give your fingers and hands nasty cuts when you grab the cut edge of a part.
Stainless steel deburring tools such as coated abrasives (belts, discs, or flap discs), nonwoven abrasives, metal files, deburring blades, and wire brushes can be used to deburr parts.
Selecting Abrasives for Cutting and Deburring Stainless Steel
You should have a few products on hand for cutting and deburring before you start your stainless steel fabrication project. Some of the products you might need include:
- Chop Saw Blades/Wheels - For cutting stainless parts from bar, tube, angle iron and other stainless steel stock.
- Cut-off or Cutting Wheels – For cutting stainless shapes. Also, useful for stainless weld joint such as beveling and cutting apart bad welds.
- Reciprocating Saw Blades – For cutting stainless steel sheet, tube, bar, angle iron, and other stock.
- Hole Saws – For notching stainless steel tube and making holes in stainless steel sheet or plate
- Non Woven Abrasives - For deburring and removing sharp edges from cut stainless steel. Nonwoven abrasives will also be useful for cleaning and surface preparation before, during and after welding as well as smoothing, polishing, deburring, and refining finishes.
- Wire Wheels and Wire Brushes - For deburring and removing sharp edges from cut stainless steel. You only want to select stainless steel wire brushes. Wire brush products are also helpful for cleaning and surface preparation before, during and after welding as well as polishing and refining finishes.
- Metal Files – Metal hand files are useful for manually deburring edges after cutting. They can be useful in reaching spots where a large wire or nonwoven wheel will not fit.
Pre-cleaning and Preparing Stainless Steel Surfaces for Welding
Like any weld joint, the surface needs to be cleaned and prepared before welding. However, stainless steel is less forgiving than carbon steel in terms of contamination from dirt, films, grease, and oil.
MIG and TIG welding requires an inert or protective shielding gas. Contaminants can disturb the shielding gas and lead to discoloration in the weld or surrounding heat-affected zone.
Abrasive grinding wheels are also important in preparing the proper fit between the parts in the joint. On larger thicknesses, the stainless steel pieces need to be beveled with cutting or grinding. If multiple passes are used, then grinding between passes may be required on flux and stick welded joints.
Stainless Steel Weld Post Cleaning and Treatment
Abrasives are an essential tool for post-treatment and cleaning of the weld and the surrounding metal.
Heat tint oxide and the chromium depleted metal below the heat tint discoloration. Pickling paste, electrochemical weld cleaners, pickling baths, abrasive blasting, nonwoven abrasives, stainless steel wire brushes, and coated abrasives are typically used to remove heat tint. The acid pickling baths and pastes contain nitric and hydrofluoric acids, which are toxic and require special measures to handle safely. Abrasive cleaning is safer and just as effective. Electrochemical weld cleaners are costly and require chemicals. In industry, a combination of abrasive grinding followed by pickling is often employed.
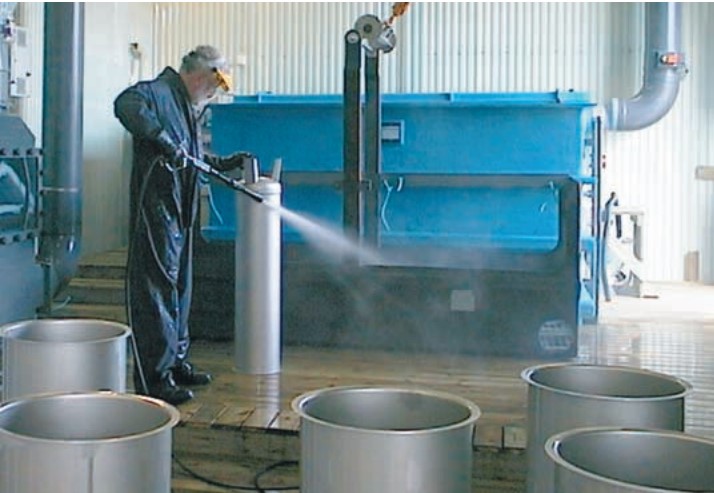
Stainless steel brushes will remove the heat tint, but they might not remove the chromium-depleted layer. Abrasive grinding with a 360 grit or coarser product should remove the chromium depleted layer and prevent rusting. Even a cut buffing step might be aggressive enough to remove the heat tint as well as the depleted layer. The heat tint is outside the weld zone, so you do not want to remove a lot of material because this reduces section thickness and therefore strength.
Sugaring is a heavier black oxide scale in the root or backside of some stainless steel welds not protected with a purging gas. Depending on the furnace atmosphere, oxide scales are also formed on stainless steel during heat treatment and forging. A more aggressive or coarser grit abrasive product is required to remove the oxide scale.
Slag, weld spatter, undercuts, cracks, pores, and other stainless steel welding defects also need to be removed with abrasives or carbide burrs.
Weld bead blending, take down, or flattening can be done with 40, 50, 60, or 80 grit abrasive disc, flap disc, or belt. Weld sugaring, heat treat scales, and weld defects could also be removed with 40 to 60 grit abrasives.
Try leveling weld or parting lines with a 60-grit abrasive product first. If metal removal is too slow, then go to coarser grits. Changing abrasive product types instead of using a coarser grit size is a better approach.
If a 60 or 80 grit size aluminum oxide abrasive product isn’t cutting it, then switch to a supersize zirconia or supersized ceramic product. These products will remove material faster without generating the deep scratches or digs caused by grinding with coarser 36 or 40 grit abrasives.
If your welds are well made and mostly flush, then an 80 or 120 grit flap disc could be sufficient to flatten and blend your welds.
While a coarser grit size can remove material faster, there are several reasons to use a finer grit abrasive when leveling and blending stainless steel welds:
- 304 stainless steel is softer than alloy steels, so coarser grit abrasives can dig or gouge more easily.
- Coarser grits tend to generate more heat and therefore more heat tint
- With the aggressiveness of coarser grit, it is easier to thin the metal surrounding your stainless weld. Thinning reduces strength.
- Chances are if you are using stainless steel, then you will want a satin or polished appearance in your final product. Coarser grits leave behind a rougher surface requiring more work and abrasive steps to remove deep scratches and generate the final required finish.
- Removal of coarse grit scratches is also important for maintaining corrosion resistance. The valley or pit of a scratch gets less oxygen and makes the metal more susceptible to crevice and pitting corrosion.
Finishing Stainless Steel
After the welds have been leveled and blended, then the required surface finish is generated in a multiple-step process.
Generating the surface finish you want on stainless is dependent on several factors:
- Types of abrasive
- Abrasive grain type and hardness (zirconia, ceramic, etc.)
- Grit size – the size of the abrasive particles
- Abrasive product form – belt, disc, nonwoven, flapwheel, buffing wheel
- Equipment type
- Force applied during finishing
- Power (Horsepower, kW)
- Abrasive surface speed
- Backup wheel or pad hardness and smoothness
Setting the Grain
Graining or setting the grain is the first step in generating a surface finish on stainless steel. Graining is developing a unidirectional scratch pattern across the stainless steel surface. This step is also known as pre-polishing, polishing, or brush finishing.
For some applications, a grained or brushed surface finish might be fine and even more desirable. Brushed stainless steel surfaces do not show fingerprints and smudges as much as mirror-polished stainless. If you mirror polish your stainless project, then you will be spending repeatedly cleaning it later.
Coated abrasive belt, drum, or disc polishing is different than producing a polished surface by buffing. Non-woven abrasives can also be used for graining, brush finishing, or pre-polishing.
Using a progressively finer series of coated abrasives can reduce the final buffing time and produce a better finish. A series of coated abrasive steps could include:
- Pre-polishing with 80 to 120 grit – your blending step after welding may have already done this.
- Polishing with 150 to 240 grit
- Final or fine polishing with 280 to 400 grit
The specific series of abrasive can vary depending on the initial roughness of your stainless steel project. You need to try a few different abrasive grit sizes and products to determine what is best for your application.
If you used 80 grit or 100 grit to flatten and blend welds, then you might be able to skip to the fine polishing step using 280 grit. A combination of 120 grit coated abrasive followed up with medium and fine nonwoven surface conditioning abrasives is another option.
With nonwoven abrasives, you could use medium, fine, and ultrafine products to polish before buffing.
If you are using a nonwoven or coated abrasive belt or drum to produce a unidirectional grain or grit line pattern, then each progressive polishing step should be done at a 90-degree angle or against the grain of the last step. This will help you recognize that you have removed the scratch pattern from the previous step. Sometimes the shape of the project or assembly may not allow this.
A brushed finish is generated with 150 to 240 coated abrasive belts or drums or medium very fine nonwoven abrasives.
A matte or satin finish is generated with a 220 to 240 grit coated abrasive or very fine nonwoven abrasive belt, drum, or disc.
Getting a High Gloss or Mirror Finish
How do you get a mirror finish on stainless steel? The short answer is through cut buffing and color buffing. These steps are used to produce a final polished or mirror finish after the initial refinement steps.
The initial or intermediate finishing (pre-polishing and polishing) steps using belt polishing, nonwoven flap wheels, or abrasive discs/pads can have an impact on the effort to produce the final finish as well as the buffed surface quality and appearance. Using a series of progressively finer grit sizes in pre-polishing steps will reduce the amount of cut buffing required.
Cut buffing or pre-polishing buffing removes finer scratches remaining after the abrasive belt or disc polishing steps. Black or black magic compound contains coarser grit emery abrasive, a mined abrasive mineral.
Color buffing is used for final polish buffing to bring out the luster and brilliance of the metal. Green rouge compound contains chromium oxide. Green rouge is also known as jeweler’s rouge. It generates gloss and polish. Blue compound contains the finest abrasive grains and is used to generate the highest gloss and a final mirror-polished finish.
Fastening, Mill Finishes, and Touch-up Finishing
While we have assumed your stainless project was fabricated by cutting, forming, and welding. Mechanical fastening is another option for assembling your project. If you use bolts, nuts, washers, or other fasteners in a marine or corrosion-prone place, then make sure the fasteners are made of the same grade stainless steel as the sheet metal, plate, or bar stock. This will reduce the change for galvanic corrosion of the fasteners.
A fastened assembly can open up new finish possibilities. A wide variety of mill stainless finishes are available for stainless sheet. Once you cut and drill holes on a mill finished sheet, you will need to deburr and touch-up around the drilled hole or cut edges. Touch-up finishing from handling and end-use might be needed on a welded project as well.
Quick change miniature coated abrasive and nonwoven discs can be a good option for deburring and touching up around drilled holes or removing scrape mark. 2” Mini Zirconia Flap Discs, 2" Quick Change Roloc Surface Conditioning Discs, 2" Quick Change Ceramic Sanding Discs, and 2" Quick Change Polish Plus Felt Polishing Discs are good to have on hand for stainless steel touch-up jobs.
Do’s & Don’ts when Cutting, Grinding, and Polishing Stainless Steel?
Overheating, Discoloration, or Burning
Don’t use dull abrasives, high speeds, or apply high pressures. These cause overheating and can result in heat tinting or discoloration and burning of your stainless parts. Discolored or heat-tinted areas can rust. If discoloration does occur, then use a new, sharp abrasive product and gently remove the discoloration.
Burning or overheating during cutting or grinding leaves residual tensile stresses on the surface and can cause the austenite to transform into brittle martensite. If your part is stressed in end-use, then then you should avoid grinding burn. Utilizing new supersized zirconia or ceramic abrasive products should eliminate grinding burn.
Avoid Excessive Pressures During Finishing or Polishing
Don’t bear down or use excessive pressure when finishing stainless steel. This can just result in more discoloration or heat tinting. Keep the abrasive product moving across the surface to prevent a buildup of heat in one area.
Don’t overwork the surface during finishing and polishing steps by using too much pressure and abrasive speed. Too much stress on the stainless steel surface during forming or finishing can cause an orange peel effect. Orange peel may need to be removed with a fine grit abrasive followed by repolishing a second time with lighter pressure or speed.
Cross-contamination with Steel
Transfer of steel or iron onto stainless can occur from steel parts and used abrasive products.
Avoid any cross-contamination of your stainless parts with steel or iron. If steel parts or tools (punches, hammers, etc.) from other projects rub against your stainless part, then they might transfer some steel to the surface, which will degrade corrosion resistance.
Sources of iron contamination to avoid include:
- Steel or iron dust from grinding carbon or alloy steel parts
- Abrasives used to grind carbon or alloy steel parts
- Steel brushes or carbon steel wool
- Use stainless steel brushes and stainless steel wool
- Steel blasting shot, grit, and tumbling media
- Vises, clamps, chains, or holders
- Carbon steel tools – hammer, screwdrivers, chisels, etc.
- Forming rolls, molds, and dies
Abrasive products that have ground steel parts on your stainless project. You should keep a set of abrasive discs, belts, and flap discs for use only on stainless. Using discs that have ground stainless to grind steel is fine.
Proper Abrasives Selection
What are the best abrasives for cutting and grinding stainless steel?
You need to select abrasives suitable for grinding stainless steel. For example, while coarser grit silicon carbide abrasive products are useful for grinding glass and titanium, they do not perform as well as alumina and zirconia in grinding stainless steel. A poor abrasive selection can lead to a quickly dulling or loading abrasive, which will stop cutting and burn or discolor the stainless steel parts.
Some abrasive products specifically suitable for stainless grinding are labeled with “Stainless” or “inox”. Inox is derived from the French word for stainless steel meaning “inoxidizable”. The abrasive products should be free from iron contamination.
The best abrasive grains to cut and grind stainless steel alloys include aluminum oxide, zirconia, and ceramic. Zirconia will outperform aluminum oxide in stainless steel applications. You should be able to grind more parts or remove more metal with a zirconia disc or flap disc before the disc just stops cutting effectively and begins to burn the metal. Ceramic abrasives have higher hardness than zirconia. Ceramic should outperform zirconia abrasives on harder to grind stainless steels like hardened martensitic grades and high nickel grades.
Supersize layers on a coated abrasive product can double the amount of metal removed or parts ground. Supersize provides a lubricating and cooling effect. This keeps the abrasive grains cutting longer before dulling and then plowing and burning the metal. The supersize also helps reduce the binding of stainless steel chips to the cutting edges of the abrasive grains.
Always start with the finest grit size recommended or try even finer. The finer grit size reduces heating and discoloration on stainless while reducing the work you have to do later to remove scratches and create a brilliant stainless steel finish.
What’s next and how can I get started?
Once you have decided what surface finish you or your customer wants on the stainless steel project you are fabricating, then you can select and order abrasive products, so they will be within hand’s reach when you have finished cutting, bending, forming, and welding.
Here is a good list of abrasive products for your stainless steel grinding, finishing, and buffing toolbox:
- Surface Conditioning Discs – For weld joint preparation and post-weld cleaning and heat tint removal
- Conical or Type 29 4 1/2” High Density Zirconia Flap Disc 40 grit and 60 grit – For heavy metal removal such as shaping stainless steel parts for joint preparation before weld, leveling oversized weld beads, grinding out large defects.
- Flat or Type 27 4 1/2” Black Hawk XL Ceramic Flap Disc 80 and 120 grit – For flattening moderately concave weld beads, shaping parts without digging, and removing oxide scale from welds backsides, forgings, and heat-treated parts, and blending.
- 4 ½” Ceramic Fiber Discs 80 and 120 grit – For flattening, scale removal, and blending where a more flexible product is required.
- 4” x 4” Interleaf Flap Wheel Drum 120 and 240 grit – For heat tint removal, deburring, and generating a directional grain on stainless steel.
- Finer Grit Abrasive Sanding Belts - For heat tint removal, deburring, and generating a directional grain on stainless steel. A series of grits sizes are needed depending on the finish you want (Brushed – 150/180 grit, Satin 180/220 grit, Matte 240/280 grit)
- 4-1/2" x 7/8" Polish Plus Felt Polishing Flap Discs – For buffing stainless to a bright luster or mirror finish with an angle grinder
- 4-1/2" x 7/8" Polish Plus XL Flat Felt Polishing Discs– For buffing stainless to a bright luster or mirror finish with an angle grinder
- Buffing Compounds – Used with felt discs and felt flap discs to buff stainless to a bright luster or mirror finish
Have more questions about abrasives for stainless steel?
Please do not hesitate to reach out to us. We know how difficult it can be when searching for the best abrasives for your job. We’re here to help guide you as best we can. Please feel free to reach out to one of our experts at Empire Abrasives, 1-800-816-3824. Whether you are experienced or a novice -- we are always happy to lend a helping hand.